Come see us at the ACCO Conference
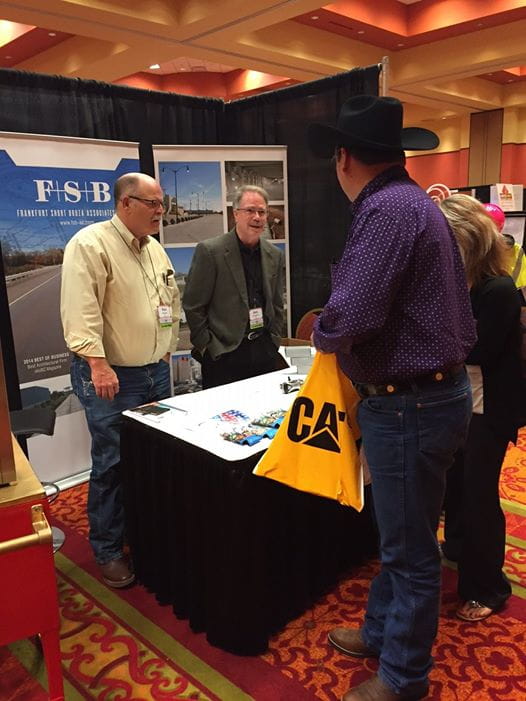
Come see us at the ACCO Conference
FSB is a nationally recognized architectural, engineering and planning firm whose mission is to provide thoughtful and creative solutions that result in quality projects for their clients. One of the factors contributing to their success is their commitment to also provide a thoughtful, inspirational and collaborative space for their staff to create such solutions.
Bentley Flooring was fortunate to get an inside view of their energizing environment when installing the new flooring for FSB’s recent “refresh” of their Oklahoma City office on the 4th and 5th floors of the Paragon Building. Several large, high-tech conference rooms provide for the interchange of ideas, as well as open work spaces wrapped in continuous windows, letting in an abundance of light and allowing limitless space for imagining.
With this renovation, FSB’s ability to collaborate is further strengthened by the addition of stand-up meeting stations and smaller traditional meeting rooms scattered throughout both floors. Each of these rooms and stations offers computer screens and all other wired technology needed for technical discussions, quick consultations or lengthier presentations. Throughout both floors, wall panels were lowered, some offices eliminated and employees within each discipline were gathered into their own distinct areas for easier communication.
We were also impressed by FSB’s serene palate of grays, blacks and charcoal inset with bold, bright bands of colors interspersed throughout the carpeted workspace. Accent colors from these bands were applied to walls and columns in the open areas.
In addition to the pleasing aesthetics, expanded café areas were installed on both floors, replacing small break areas which would only accommodate a few people. Each café features bistro-type seating, a large-screen TV, vending machines, multiple microwaves and oversized refrigerators, to accommodate the increased number of workers. These areas have become a popular place for staff to gather and for employees from different disciplines to get acquainted and build camaraderie.
Even the 4th floor restrooms were updated and refreshed.
The renovation will potentially benefit more than FSB employees. Two large conference areas were added to the fifth floor, with the capacity to hold about 40 people and 25 people respectively. These rooms are used not only for company training and client meetings, but they also are available for organizations affiliated with FSB or its employees.
Thank you, FSB, for the opportunity for Bentley Flooring to provide our services to one of our valued architectural partners.
Since the space race of the 1950s and 60s, politicians and economists alike have linked math and science education with the United States’ ability to compete on a future global stage. In the 1990s the National Science Foundation coined the acronym “STEM”— science, technology, engineering, math —in an effort to emphasize their co-dependence. Now a commonplace term, STEM has come to represent interdisciplinary education and the real-world application of math and science principles.
OKLAHOMA CITY – Jason Andrews said he can hear an earthquake, like a large truck, before it hits. Then, he feels a wave pass through Langston’s Town Hall, passing from southeast to northwest.
“When you have a little shaker, you see small cracks that weren’t there before,” he said.
Dozens of quakes have caused minor damage at his home and at work, where he is the city’s code enforcer. He noticed another hairline crack on the Town Hall ceiling on Friday he hasn’t seen before. Scientists who study Oklahoma’s dramatic temblor increase are calling for more research on damage from lower-magnitude shaking Andrews and other residents feel.
Oklahoma Geological Survey Director Jeremy Boak said personal descriptions of events improve his agency’s research. He needs residents to report the earth’s shaking to understand how those quakes behave. The Sooner State’s temblors are likely triggered by oil and gas wastewater injection. But the motion is generally shallower than naturally occurring quakes, so seismic waves travel farther, according to national research published in October. Residents contacted Boak describing damage at their own homes, so there’s a broad perception the ground shaking could have a cumulative effect, he said. His agency is working to understand how to mitigate earthquake risk and what damage could occur.
“I think it would be good for the state to do a formal analysis,” he said. “We need to begin to make the effort to say, ‘What do we know?’”
Boak said he would like to provide a hazard assessment. But he needs structural engineers’ expertise to determine the extent of the problem. OGS recorded 960 quakes magnitude 3.0 and larger in 2015, he said. It recorded about 30 events magnitude 4 and larger. The Oklahoma Department of Transportation inspects roads and bridges within a 5-mile radius of any quake that’s a 4.0 magnitude or larger. It expands its inspection radius if any damage is identified, said spokeswoman Brenda Perry. The agency hasn’t found major damage in recent years, she said. Inspectors did find minor damage to Highway 62 after the 5.6 magnitude temblor in 2011. ODOT is working with contractor Infrastructure Engineers Inc. to review the agency’s inspection procedures. The analysis will help guide the agency to formalize a response policy for quakes, she said.
University of Oklahoma assistant professor of civil engineering Phillip Scott Harvey Jr. is one subcontractor examining ODOT’s procedures. The research team is examining the cumulative effect on state infrastructure from repeated, low-magnitude temblors, and if that could be as damaging as a large quake, he said. Harvey’s work will also provide recommendations on how far inspectors should look from earthquake epicenters.
Benjamin Wallace said there’s likely not a cumulative effect on commercial buildings. The structural engineering director at architecture and engineering firm Frankfurt Short Bruza said new structures are built to codes that include seismic hazards.
“We don’t worry about small windstorms creating cumulative damage,” Wallace said, so he wouldn’t be concerned about small quakes either.
Old, unreinforced masonry buildings may experience cracks in bricks and drywall, he said. Minor quakes, those less than magnitude 4.0, won’t cause catastrophic damage or cumulative failure to structures, he said.
Heavy structures are also more likely to receive damage. A brick spire at St. Gregory’s University was damaged in the 2011 quake near Prague. In Guthrie’s downtown, in which many buildings were built around the turn of the 20th century, those structures have been weakened over time from weather, Wallace said. Employees at several businesses in Guthrie’s historic downtown said they have seen cracks in drywall. Old buildings weren’t designed to withstand seismic forces, so they could face deterioration from minor shaking. A larger temblor could cause damage to already-weakened structures, Wallace said.
“If induced earthquakes caused a larger earthquake than was anticipated before, that would concern me,” he said.
Boak said he would like to gather a consortium of structural engineers, hydrogeologists and petroleum geologists to study and publish what is known. The state may need to take a different approach if researchers don’t find cumulative damage effects, he said.
“If we investigate and find we have a relatively limited number of cases, we may have to look at this on a case-by-case basis, rather than a huge class of property owners in Logan and Payne counties to demonstrate that damage,” he said.
Want to see information about real-time earthquakes, an online catalog search of archives, seismicity maps and statistics? Visit http://earthquake.usgs.gov/
“If we could see three-dimensionally into the ground, we would be scared, wouldn’t we?” said Wes Brannon, construction administration for Frankfurt Short Bruza Architects and Engineers.
The PVC pipe is part of a geothermal system where 101 wells will be used to heat and cool the new 70,000-square-foot public safety center instead of a typical heating and air conditioning system. The new home of police headquarters, the 911 communication center and emergency management operations is the third city-owned building to use a geothermal system. The Mitch Park YMCA and the Cross Timbers Public Service Center were the first two city buildings to use geothermal energy, which uses the earth’s relatively constant temperature to provide heating and cooling for residential and commercial buildings.
In Edmond’s system, water is circulated through plastic pipes buried beneath the earth’s surface. During the winter, the fluid collects heat from the earth and carries it through the system and into the building. During the summer, the system reverses itself to cool the building by pulling heat from the building, carrying it through the system and placing it in the ground.
“A lot of people don’t understand geothermal,” said Glenn Fisher, Edmond Electric director. “There is nothing magical about it. No abracadabra about it. You are just changing one heating and cooling system for another. It’s not magic by any stretch of the imagination.”
The advantage of a geothermal system is it is cost-effective, reliable, sustainable and environmentally friendly, city leaders said. The public safety center geothermal system will cost $1.25 million.
Brian Sauer, principal and licensed mechanical engineer for Frankfurt Short Bruza, said the public safety center will recoup the cost two or three times faster than most similar systems because the building will run 24 hours a day. The average building has a payoff in the five- to 10-year range.
“This building will pay back faster because the building never really sleeps,” Sauer said. “A typical office building runs eight hours and gets a break. This building will get a payback in a couple of years.”
The system will save energy and reduce the city of Edmond’s electricity costs. Fisher estimates the geothermal system will save between 25 and 35 percent on electrical costs. He said he hasn’t calculated an exact dollar figure. About 72 percent of Edmond Electric’s budget goes to wholesale energy costs.
“It helps us shave our summer peak,” Fisher said. “OMPA (Oklahoma Municipal Power Authority) billing requires you to pay a certain percentage of the peak the year round. Anything that shaves the peak helps the year round.”
The public safety center geothermal system has been a challenging project. Sauer estimated 50 architects and engineers at FSB played a role in the design of the two buildings that will make up the $28.6 million public safety center complex. A second structure, the former Edmond Electric building, is being renovated to give the police department the 15,000 square feet of space it needs for laboratory work and to store evidence.
Voters approved in 2011 a half-cent sales tax to build the public safety center.
Sauer said about 10 engineers worked on the mechanical design of the buildings.
“This is a large effort, a challenging project because of the lack of space and the functions of the building are unique, totally different.”
The spec book for the design of the public safety center is one of the largest composed by Frankfurt Short Bruza.
“I think this is an entertaining project with challenges and sustainable technology,” Sauer said. “We have had the support of the city of Edmond. On some projects, people look for ways to save money by not doing this system. It is good to have their support.”
Challenges and surprises surfaced while installing the well fields. In the former bank parking lot, workers found portions of a porch or basement that had to be removed and hauled off which turned out to be costly, said Deputy Police Chief Steve Thompson.
“It was kind of a surprise,” Thompson said. “We didn’t see that one coming. Look at how old this is here. You are right off Highway 66. Who knows what you are going to find?”
City leaders speculated it could have been a house or a gas station from the 1950s or 1960s. The soil in that area had to be removed and new dirt brought in to protect the new pipes.
“You want to avoid rocks and things like that because you want to protect the pipes,” Fisher said. “You want to have a clean field above these lines.”
The flexibility of the pipe underground in the sand also helps to protect the system from earthquakes, Brannon said. The public safety center is expected to be complete by July or August.
Frankfurt Short Bruza (FSB) was selected as the recipient of OKC Beautiful’s 2013 Community Spirit Award for its donation to the Myriad Botanical Gardens.
To commemorate its 65 years in business, FSB donated $50,000 for the acquisition and placement of 65 trees for the Myriad Gardens.
A luncheon honoring FSB and other award recipients is scheduled March 28 at the Oklahoma City Golf and Country Club. For information on the 30th Distinguished Services Awards Luncheon, visit okcbeautiful.com.
By Bridget McCrea
Trying to piece together a dome on top of a building is a lot like putting pieces of pie back into a pan: The task starts out relatively easy, but becomes progressively harder as the structure takes shape. “It’s not the first piece that bothers you – it’s the last one,” says John Jamison, project executive at Oklahoma City-based Manhattan Construction Co.
And Jamison should know. His firm, along with Tulsa, Okla.-based Flintco, came together in a joint venture known as “Capitol Dome Builders” to construct a dome for the Oklahoma State Capitol building. A monumental undertaking, the project required more than 1,200 precast concrete pieces that altogether weighed more than 1,300 tons: The heaviest pieces weighed almost 8 tons. These pieces contributed to what is now an 80 foot-diameter-dome, which projects 157 feet above the existing roof and weighs more than 2,500 tons.
Hoisting the panels 280 feet in the air, then situating them one-eighth of an inch away from one another around the entire circumference of the dome was no easy task, says Jamison, particularly when it came down to the last few pieces. “We didn’t have a saw or jack hammer to get them in place,” he recounts, “so it had to be perfect all the way around, or we knew we’d have a problem in the end.”
Thanks to the controlled environment of manufacturing and curing the panels at a precast plant – Arkansas Precast and Structural Stone LLC, of Jacksonville, Ark. – Jamison says those final moments of completion went without a hitch. Additionally, he says precast ensured flexibility when shaping the dome, durability, speed of construction and precise color matching with the existing structure.
“We put a lot of effort into matching the color of the building – but what color do you put on a building that’s 87 years old?” Jamison asks. “By combining technology with the precast – with its adaptability of colors – we were able to find the right match.”
Dusting It Off
For much of the 20th century Oklahoma’s state capitol operated in an “unfinished” state due to a lack of funding and steel spurred by World War I. Though the capitol itself was completed, the limestone dome with its cast-in-place concrete structure as envisioned by the original architects in 1914 never came to fruition.
That was, until the state dusted off those original plans and decided that the structure should be completed by the state’s centennial in 2007. Six years ago, Frankfurt-Short-Bruza Architects P.C. of Oklahoma City completed a feasibility study for the project and determined that the existing structure could indeed support a dome. At that point, the Oklahoma state legislature approved an act that would allow the project to proceed using a design-build process.
Before construction could begin, the dome would be redesigned to include the latest building materials. “We changed a lot of systems,” says Jamison. Concrete frame and ashlar stone, for example, was changed to precast concrete. The switch helped lighten the structure considerably, says Jamison, and allowed the builders to match the new dome’s colors to the existing limestone-covered building.
Construction began in April 2001 and finished in November 2002, just in time for Oklahoma’s Statehood Day. During that 18-month stint, the capitol remained open and two different legislative sessions proceeded in a “business as usual” fashion. “The building never shut down,” says Jamison.
When the original saucer dome was removed, it left behind a 80-foot-diameter hole in the top of the building, which was sealed by closing off an area of the capitol, then soundproofing it. Additionally, various historic murals and a stained-glass skylight had to be protected from damage during construction.
“Due to these and other factors, we had to build everything up and out,” says Jamison. “This project was about creating a logistical solution: how to get the panels to the top, how to keep the building in operation and make sure that the open hole in the roof remained watertight and secure.”
Precast, Please
Before any precast panels could be installed on the dome, the construction team had to erect a 280-foot-tall freestanding tower crane with a 230-foot boom length. With it, they were able to raise the panels, each of which weighed more than 15,500 pounds, and then position them around the dome. The precast portion of the project took about a month, says Tim Dolf, senior structural engineer at Frankfurt-Short-Bruza Architects.
Dolf says precast made the most sense by today’s standards compared to limestone, which he calls “the only other alternative.” It was historically necessary to make the dome look like the original limestone material, says Dolf, and that made precast the most practical alternative. “The decision to use precast was made almost instantaneously,” he adds. “We had complete confidence that we could make it work.”
In addition to the panels, Arkansas Precast delivered approximately 800 precast pieces, including ornate items, to the job site. Using the materials helped cut down on overall construction time and guaranteed durability and a finished building that looked to be constructed of the same material, despite the fact that its major components were built nearly a century ago.
Jamison says the design-build team added components like silicone sealant, epoxy-coated rebar and stainless steel connections to the precast structures in order to create a “100-year structure” and guarantee adequate waterproofing.
“We didn’t want to worry about rusty connections or the penetration of water through the panels,” says Jamison.
“It was all handled very easily at the precast plant, and when they arrived on the job site all of the molds, shapes and sizes fit perfectly with what we were looking to do.”
Although construction of the dome progressed as planned and finished ahead of schedule, Jamison says the project was delayed somewhat by Mother Nature. Wind was the biggest issue, he says, since erecting heavy precast panels 280 feet in the air is not an option when the wind reaches 50 mph. He estimates that the job was shut down for about 45 days due to such forces.
“At times, we had crews out there working at 2 a.m. because the wind had subsided,” says Jamison, who calls the overall project a tremendous success based on the fact that it was finished under budget, ahead of schedule and beyond expectations. The latter is particularly important since the project had more than its fair share of opposition.
“A lot of Oklahomans thought it would be ridiculous to add a dome to the capitol now, 90 years after the building was constructed,” explains Blake Wade, executive director of the Oklahoma Capitol Complex and Centennial Commission. “Today, I can honestly say that it exceeded the expectations of the entire state, and that it’s now the No. 1 tourist attraction for our great state.”
Wade credits precast concrete with helping to make the dream a reality and with an affordable, manageable and enduring product. “It was a thrill to be able to work with all of these fine companies,” says Wade, “and know that because of precast, it was all able to get done,” he says.
Jamison says the camaraderie of the group that designed and built the dome was above par and resulted in such a successful project that he’d do over again, if he could – despite the challenges that could come from trying to get that “last piece” in place. “We’d like to build another dome,” he says, “but that’s the last one for Oklahoma.”
– Bridget McCrea
“If you don’t have that experience and familiarity with federal regulations or LEED standards and you try to learn it on the job, you’re in trouble—you won’t be able to properly focus on the client’s project,” FSB Federal Market Principal Gene Brown said. “That’s just something you have to know in advance. Our team is very detail-oriented, and we fully embrace the regulatory challenges.”
Government agencies typically require new facilities to be built to high standards of sustainability in accordance with Leadership in Energy and Environmental Design (LEED), a rating system to evaluate the environmental performance of a building and encourage sustainable design. Brown said the federal government began using LEED in an effort to demonstrate environmental stewardship without having to maintain their own independent rating system. The number of LEED points a facility receives determines its LEED rating level, either Certified, Silver, Gold and Platinum. It is a holistic rating system covering everything from energy efficiency to sustainable building materials. For example, a building might receive four LEED points under the water efficient landscaping credit and another point for encouraging building occupants to bike to work by offering bike storage and changing rooms with showers.
“When FSB plans to meet a certain LEED level for a federal client, we always ask ourselves what credits make the most sense for our client and the building’s environment,” Brown said. “The federal government’s budgets are often tight and scope is driven by mission, so we aren’t able to add cost to the project just in the name of sustainability alone. We work hard to be fiscally responsible by finding those sustainable solutions that are also life-cycle cost effective and support the federal government’s mission.”
Silver to Gold: Improvising additional sustainable features mid-project
Creative sustainable design abilities are indispensable when architects and engineers must amend building designs mid-project. This flexibility was required when the Navy’s sustainability standards changed from LEED Silver to LEED Gold during FSB’s design phase for a project in Coronado, California. Although the design was sixty percent complete, FSB was asked to augment the building’s plans to achieve the new LEED Gold standard and at the same the budget was cut approximately five percent.
Because of their expertise in federal regulations and LEED standards, FSB was able to improvise to provide additional sustainable features and maintain the project’s schedule. One part of this solution was to provide the absolute minimum parking capacity required for the current facility; by not paving additional areas the project team was able to both reduce construction cost and add two LEED points for reducing impermeable surfaces. In the end, FSB was able to successfully achieve the Gold rating and provide all mission-required scope while continuing to honor the original unique design aesthetic, which reflected the rich history of the Naval Air Station.
When the building opened in May 2014, it was equipped with solar panels to provide both renewable energy and heating of water. The building’s energy consumption was reduced through the use of a well-insulated building envelope, light-reflective roofing, energy efficient heating/cooling equipment and daylight harvesting to name a few. Water consumption was reduced through the use of low flow fixtures and water efficient landscaping; storm water was collected and treated on-site through permeable paving areas and landscaping features called bioswales.
For its creatively achieved sustainable design, the project received a 2015 Federal Energy and Water Management award.
When Department of Defense clients need defending
Brown said because of the firm’s decades of experience designing for federal clients, combined with their efforts to keep on top of rule changes and updates to code, FSB tends to know regulations as well as, or in some cases even better than the regulators. This knowledge was put to use in 2016 when the firm was submitting an Air Force hangar in Little Rock, Arkansas for LEED Silver certification.
To achieve Silver, FSB incorporated materials made with recycled content and locally sourced to reduce related carbon emissions. The designers required their construction teammates to reduce construction wastes possible by diverting as much as possible from landfills by recycling. For these and many other actions, the project would be able to achieve the required points toward its goal of Silver.
When the U.S. Green Building Council (USGBC) reviewed the design-related credits, it initially denied several energy points instrumental in achieving Silver certification. FSB appealed this decision on the grounds that the cited LEED criterion was developed based upon an office building and not that of a similarly functioning aircraft maintenance hangar. FSB then referenced and proposed the proper criterion which should have been considered as the basis during the review of the team’s energy analysis. The combination of diligent documentation and a deep understanding of the energy codes and rating system helped convince the USGBC to grant the Department of Defense’s project the energy credits it deserved which led to the hangar being able to achieve LEED Silver certification.
“I think the big secret is knowing the requirements and expectations better than the people who are charged with enforcing them,” Brown said. “And not only can FSB’s architects and engineers sustainably design in accordance with the intent of LEED—we can partner with our clients to help guide them through the numerous requirements, decisions and, when necessary, we can defend their projects.”
Interested in learning more about sustainable design and your next project contact:
Federal Market Principal, Gene Brown, PE, LEED AP BD+C at federal@fsb-ae.com or directly at 405.840.2931
Overview
• Privatization Summary
• Utility Master Plan Purpose
• Utility Master Plan Analysis
• Central Plant Design
• Utility Distribution Design
• Construction Progress
• Program Timeline
• Successes and Challenges
• Q&A
Presented at IDEA 2016 Conference in St. Paul, Minnesota by:
James Rosner, PE, CEM
Director of Energy Services, Oklahoma State University
Brian Sauer, PE, LEED AP BD+C, CxA
Utility Master Plan Project Manager/Principal, FSB
Mike Isch, RA
Central Plant Project Manager, FSB
Justin Grissom, PE, CEM, LEED AP
Utility Distribution Project Manager, Burns & McDonnell