“We shape our buildings, and afterwards, our buildings shape us.” — Winston Churchill
This quote may be equally applicable to the interior design of buildings as it is the exterior, according to FSB Senior Design Project Manager John Osborne. In the past decade, business owners have witnessed work environments change significantly to become central to employee contentment and productivity.
“Most of corporate America spends their workdays indoors. From an interior designer’s perspective, this creates tremendous opportunity to meaningfully impact people’s lives.”
Interior environments impact our state of mind, level of performance and even our health. Now more than ever, the office environment is a major factor influencing employee recruitment and retention.
Autonomy and flexibility are in
In an effort to recruit and engage employees, business owners are placing new emphasis on autonomy and flexibility. Recent office interior design trends reflect this philosophy.
Mobile working and desk sharing can help reduce required leasable areas and have become a great solution for accommodating remote team members for short periods of time. Corporate clients are asking for renovations or new spaces that provide employees more options in response to the increasing value many workers place on work-life balance.
Many offices need teleconferencing capabilities and wireless connectivity. Nearly all need team spaces varying in size and formality. Open spaces and shared work environments create a synergistic, collaborative environment that enclosed offices simply don’t provide.
“A break room, conference room and private offices are not enough anymore,” Osborne said. “Modern offices need to cater to varying work styles and multiple generations.”
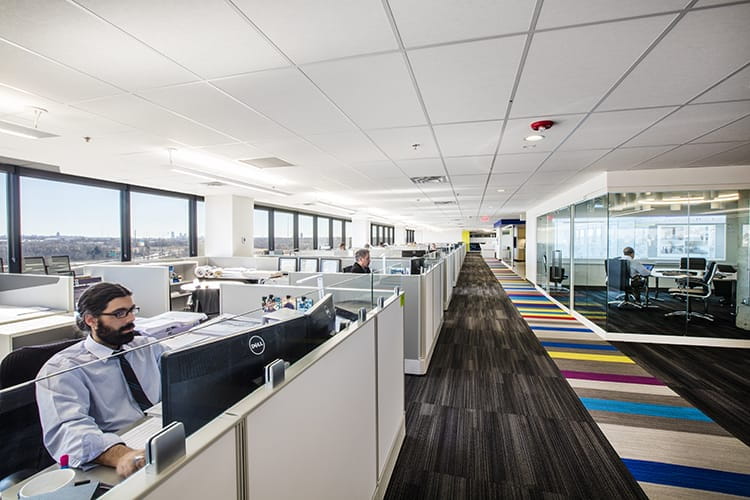
As a result of differing traditions and expectations, Baby Boomers, Gen X, Gen Y and Gen Z employees each tend to prioritize workplace needs differently. Interior spaces must not only be flexible enough to accommodate generational preferences and varying work styles, but also to enable change within the organization including new technology, a rapidly growing staff or churn.
Other more qualitative trends center around light and color. More offices are prioritizing natural light, which has been connected with better sleep cycles and less absenteeism. Some are paying more consideration to color, which can affect mood and productivity. For example, green can be calming and reduce eye strain, helpful for people who work long hours.
“Our first priority is to create functional spaces that support and enhance productivity, workflow and user experiences, and clients also depend on us to keep up-to-date on corporate interior design trends,” Osborne said. “We can help clients invest budgets wisely and come out of their renovations or new builds with interior work environments that will support and appeal to employees now and for many years to come.”
Cross-discipline team delivers more cohesive interiors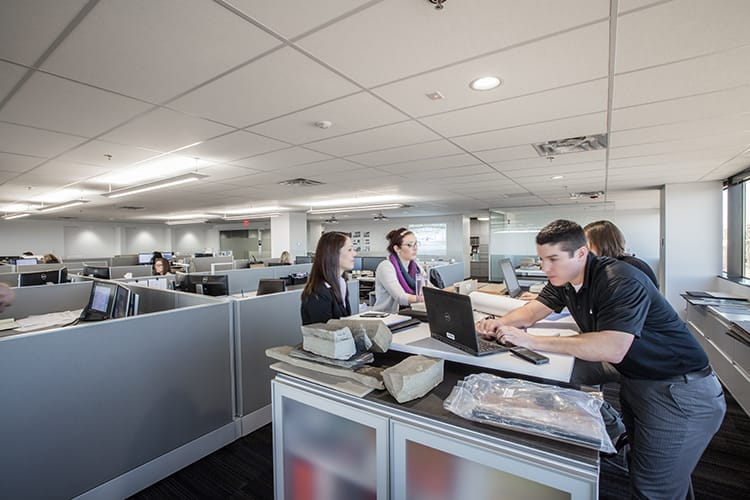
FSB typically begins every design project by developing an understanding of project goals, budget constraints and functional criteria to be incorporated into a design solution. Participating in charrettes or programming workshops is one efficient technique for accomplishing this understanding. These workshops are usually multiple-day sessions wherein FSB’s designers interface with client stakeholders to identify project design goals and requirements. This helps each team member on a project to develop an understanding of the design direction, priorities and values, and contribute throughout the process.
Because FSB is a full-service, multi-discipline architecture and engineering firm, the company’s approach is holistic—early collaboration between engineers, architects and designers allows for a cohesive design solution. Interior designers work alongside architectural designers and engineers throughout the project from pre-design through completion.
Tribe embraces open, collaborative workspace
It took this brand of true cross-discipline coordination to deliver a cohesive headquarters building to the Choctaw Nation. FSB’s project team needed to create a space that celebrated the tribe’s heritage and respect for nature throughout the campus, including interiors. The interior designers on the larger project team had also planned a modern, flexible work environment for staff catering to diverse generations and workstyles. Lastly, the design would need to be durable, low maintenance and sustainable, a priority motivated by the tribe’s environmental and financial stewardship goals.
“We always try to offer multiple options,” Osborne said. “It’s important to, above all, respect clients’ values and priorities, but this can often be achieved in a variety of ways. The merits of each option are discussed and evaluated against their respective costs to help our clients come to the best decision.”
The Choctaws had the opportunity to review color boards, material samples and 3D renderings in order to better envision the final product. They also accompanied the design team to several office furniture manufacturers’ headquarters to learn more about trends as well as to see first-hand the available options. The resulting interior was an extension of the exterior architectural design concept—a modern expression of the tribe’s long-held values and beliefs, incorporating the trend for flexible, open workspaces.
Dated office building converted to prime real estate
“Class A” office space, defined in real estate as space with modern finishes, onsite restaurants or cafes, fitness centers and covered parking, is in high demand. Caliber Development, a real estate investment company, understood this demand and enlisted FSB to renovate their recently purchased office building in Oklahoma City.
“The goal was to take a Class B or C, outdated 1976 office building at 60 percent occupancy and convert it to a successful, aesthetically pleasing space full of satisfied tenants,” Osborne said. “The 10-story atrium was a grand space flooded with natural light. So, it had a lot of potential. Still, before the renovation it felt a little cold, almost institutional, because of the finishes. The challenge was to find the balance between respecting the bones of the architecture while modernizing the space and creating an environment that would meet the market demand for more functional amenities and comforts at the office.”
To bring more warmth to the space, the team created contrast with black granite flooring and a warm wood panel system. Stone was incorporated into the atrium area to bring more warmth and texture and carried through into the newly created café for a richer, more welcoming aesthetic.
Osborne said once the renovation was complete, the building quickly reached 100 percent occupancy, and just four years later, Caliber sold the building for a significant profit, demonstrating the impact interior design can have on a client’s profitability and occupancy. The renovated office building now houses IBC Bank’s Oklahoma headquarters.
“The final result was a very successful project,” Caliber Companies President Matt Austin said. “Without hesitation, I would recommend FSB to anyone looking for a full-service architectural design and engineering firm for their office design needs.”
Interested in learning more about interior design trends and how FSB can help you on your next project, contact Laure Majors at busdev@fsb-ae.com or (405) 840-2931.